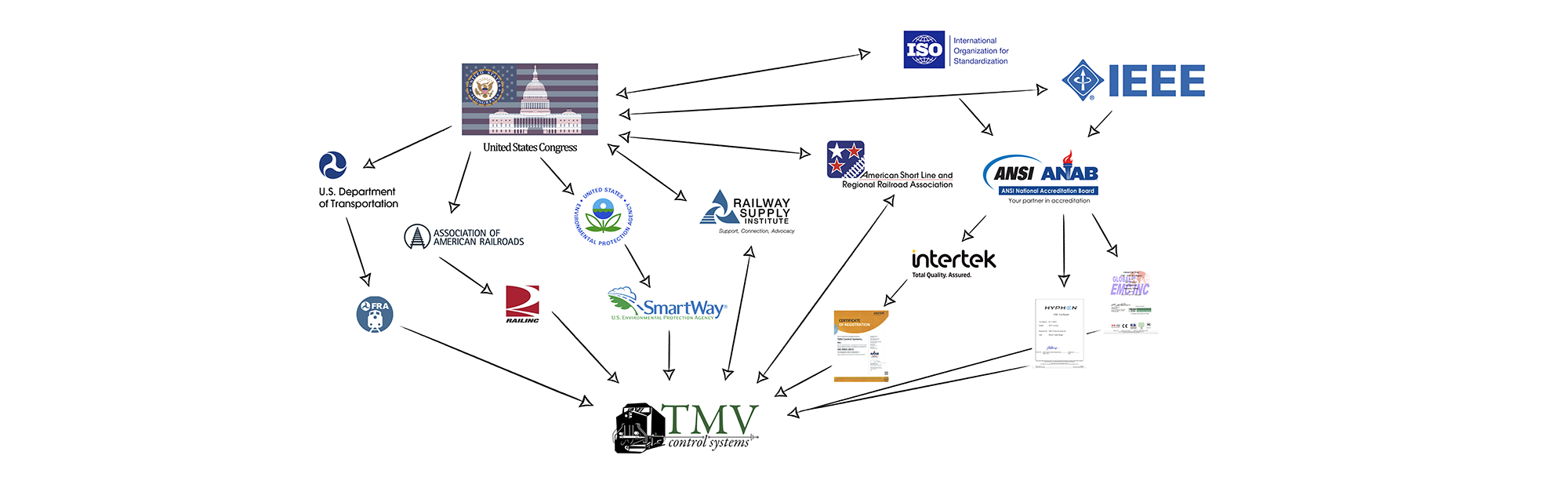
Railinc, Environmental Protection Agency, Smartway, Railway Supply Institute RSI,
International Organization for Standardization ISO, IEEE, ANSI, ANAB, ASLRRA
The Railroad Industry in North America
North America has long worked to set up a structure to help ensure companies deliver the kind of quality they promise.
This structure includes government, regulatory bodies, and associations; all their policies, means and tools by which they implement their vision. It is the framework supporting the rail industry, and therefore the scene of TMV’s operations. To build a reputation in this setting, TMV invests abundant effort into the connections that are important to our customers.
Whether it be obtaining ISO certification, meeting industry standards, fulfilling precise specs, or renewing our membership in key associations, TMV is constantly motivated by our customers’ expectations and ambitions.
Getting Certified
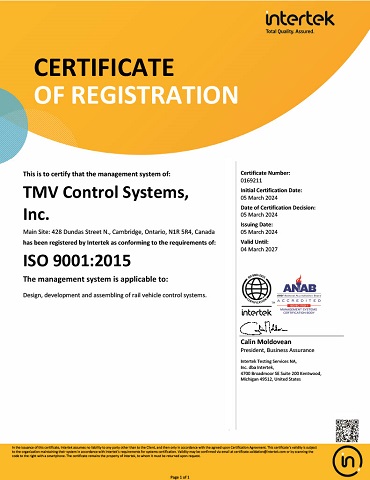
This is to certify that the quality management system of
TMV Control Systems, Inc.
has been assessed and registered by Intertek as conforming to the requirements of
ISO 9001:2015
The quality management system is applicable to
Design, development and assembling of rail vehicle control systems.
In early 2014, TMV had a customer ask us about ISO. Would we ever consider getting certified? TMV discussed it and concluded, yes!
As a B2B company, whatever legitimacy we have will help our customers’ businesses, and ISO is recognized all over the world as a barometer of essential standards, gleaned from their wealth of international experience.
TMV is proud to carry this certification, from November 10, 2014 until today. Every year we rally our efforts for internal audits, record keeping and improvements to the entire scope of our system and organization.
Noticing and Making Notes
The first step to change is always noticing. Nothing in an organization can be improved unless someone first notices and then starts the process. After noticing, the second step is good record keeping, or making notes. Renewing our ISO every year reminds us to pay attention and write it down. Through this process, our focus returns to improving our MO; in the realms of design, production, customer service and our workplace.
Good companies produce good products.
Every week, TMV holds Production Meetings. These are so everyone can keep up with current projects, called “kits” at TMV. Any issues brought up by customers during the week will be communicated and discussed during the production meeting, solutions found, and tasks divided among employees.
Any issues brought up are written down and tracked. This way we can make sure problems are halted in their tracks and won’t recur. It’s also a great way for TMV employees to share experience, so we can learn together and be a company made up of Problem Solvers.
Please feel free to Contact anyone at TMV for customer support. Have a locomotive electrical problem you just can’t figure out? We have a team brimming full of expertise who are more than willing to help.
Thank you for reading, for other articles in the series:
Introduction – TMV Claims to Pass Muster
Pass Muster – 1 – Capability Test Report for Nippon Sharyo
Pass Muster – 3 – Trade-shows and Memberships
Pass Muster – 4 – Meeting Customer Specs
Conclusion – Quality Policy and the Workplace